Emulsion Coating Machine |
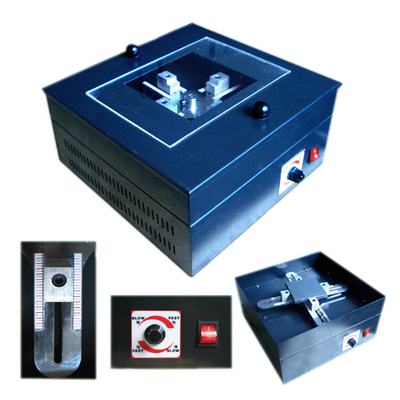 |
Steel plate coating machine can coat photosensitive liquid evenly on surface of steel plate or steel blade by the centrifugal effect caused by high-speed rotation. It is one of the important equipments in the process of plate making and a necessary tool for making high quality plate.
-
Coating by centrifugal rotation, even and flat.
-
With special designed scale, it is easy to install steel plate, which extraordinarily solve the departure in installing.
-
Collocated with speed¨Cadjustable motor, you can adjust speed of the motor with potentiometer to control thickness of coating.
-
With special designed ¡°+¡±construction, it is more saving of power and easy to clean.
-
Equipped with handle and protection cover, it is safer to operate.
- Suitable steel plate size:3.5"-8.66"(89-220mm)
- Machine size: 13.6" X 13.6" X 7"(345x345x175mm)
- Net weight: 22LB(10KG)
- Shipping weight: 24LB(11KG)
¡¡ | How the process works
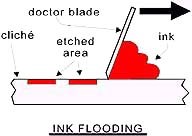 |
Step 1: Flooding
The image to be transferred is etched into a printing plate commonly referred to as a cliche'. Once mounted in the machine, the cliche' is flooded with ink. The surface of the cliche' is then doctored clean, leaving ink only in the image area. As solvents evaporate from the image area the ink's ability to adhere to the silicone transfer pad increases. |
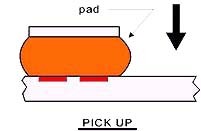 |
Step 2: Pick Up
The pad is positioned directly over the cliche', pressed onto it to pick up the ink, and then lifted away. The physical changes that take place in the ink during flooding (and wiping) account for its ability to leave the recessed engraving in favor of the pad.
|
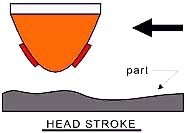 |
Step 3: Print Stroke
After the pad has lifted away from the cliche' to its complete vertical height, there is a delay before the ink is deposited on the substrate. During this stage, the ink has just enough adhesion to stick to the pad (it can easily be wiped off, yet it does not drip). The ink on the pad surface once again undergoes physical changes: solvents evaporate from the outer ink layer that is exposed to the atmosphere, making it tackier and more viscous.
|
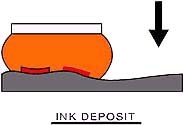 |
Step 4: Ink Deposit
The pad is pressed down onto the substrate, conforming to its shape and depositing the ink in the desired location. Even though it compresses considerably during this step. a properly designed pad, in fact, will never form a 0-degree contact angle with the substrate; such a situation would trap air between the pad and the part, resulting in an incomplete transfer.
|
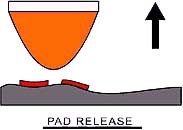 |
Step 5: Pad Release
The pad lifts away from the substrate and assumes its original shape again, leaving all of the ink on the substrate. The ink undergoes physical changes during the head stroke and loses its affinity for the pad. When the pad is pressed onto the substrate, the adhesion between the ink and substrate is greater than the adhesion between the ink and pad, resulting in a virtually complete deposit of the ink. This leaves the pad clean and ready for the next print cycle.
| |